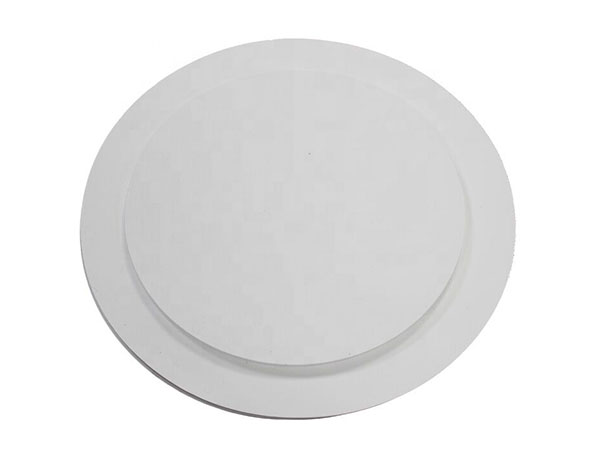
Expanded PTFE Gasket
Expanded PTFE Gasket is cut from Expanded PTFE gasket sheet, our expanded PTFE gasket sheet made with only pure PTFE resins. It is suitable for use in steel flanges as well as flanges where a highly compressible gasket is required. Expanded PTFE Gasket is also suitable for sealing flanges with irregular surfaces. It will not exhibit the cold flow problems associated with virgin PTFE or the hardness problems of some other filled PTFE products. It has excellent sealability, cuts easily, and separates cleanly from flanges after use
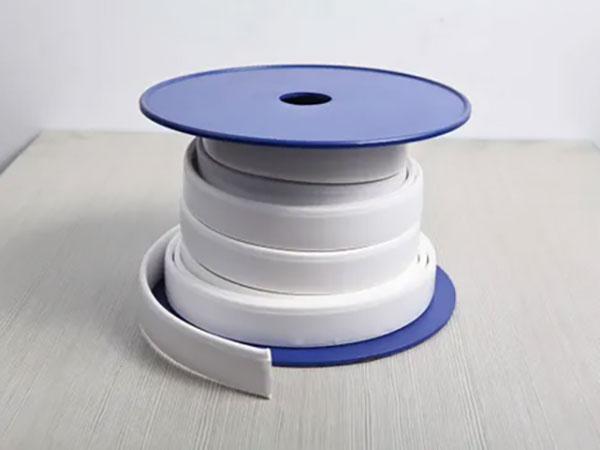
Expanded PTFE Joint Sealant
Expanded PTFE joint sealant tape is a new soft tape gasket product made of 100% PTFE. which is developed by using a highly specific treatment on the PTFE Fluorocarbon material. It is a form-in-place gasket, so it nearly can be used on any sealing surface. Especially for the irregularities and damaged flange surface. It is supplied with a self-adhesive backing for easy fitting.
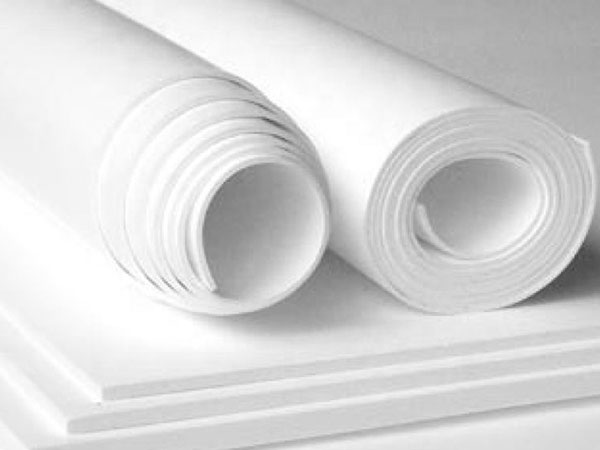
Expanded PTFE Sheet
Expanded PTFE Sheets are made from 100% virgin PTFE resins. Expanded PTFE sheet using a special process that produces a uniform and highly fibrillated microstructure with a great lot of fibres running in multi-direction. It is food approved product and has excellent resistance to a wide range of chemicals, making it a popular sealing material in the food, drink, and pharmaceutical industries. It has excellent sealability, cuts easily, and separates cleanly from flanges after use.
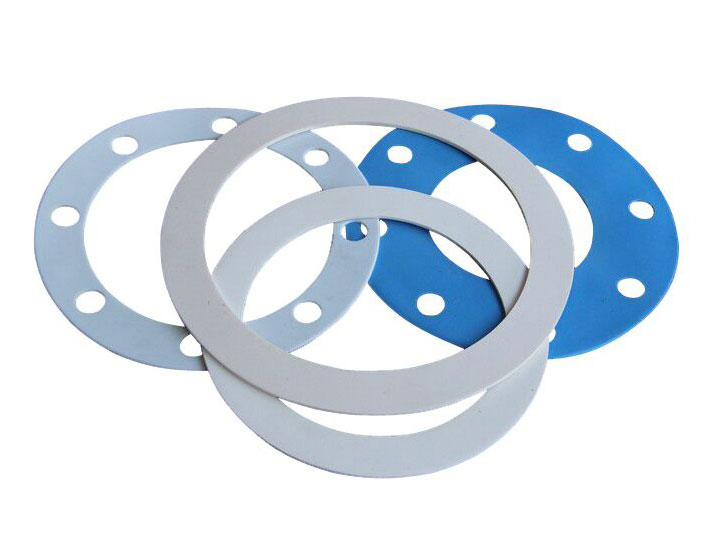
Modified PTFE Gasket
The Modified PTFE for use as a gasket material with strong chemical resistance properties and designed for severe chemical service, colour-coded for easy identification, superior seal-ability, which helps reduce process and media loss as well as fugitive emissions, reduced creep, and cold flow characteristics. The different combination offers a variety of different properties as the following sheet.
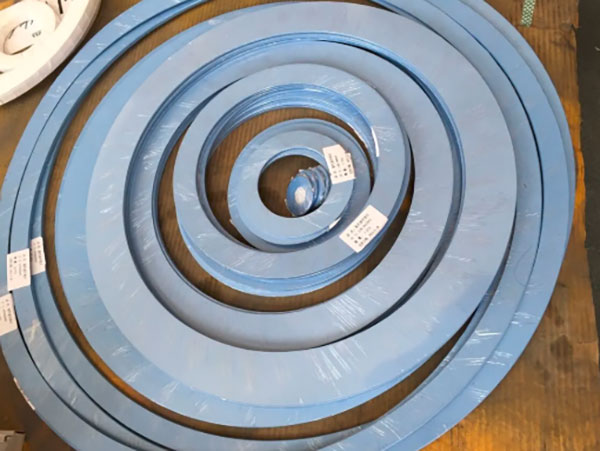
Modified PTFE Sheet
Modified PTFE sheets improved performance over conventional PTFE, Reduced product loss, and emissions. Excellent bolt torque retention, unique manufacturing process minimizes cold flow problems typical of skived and expanded PTFE Sheets. Withstands a wide range of chemicals for extended service life in a wide variety of applications.
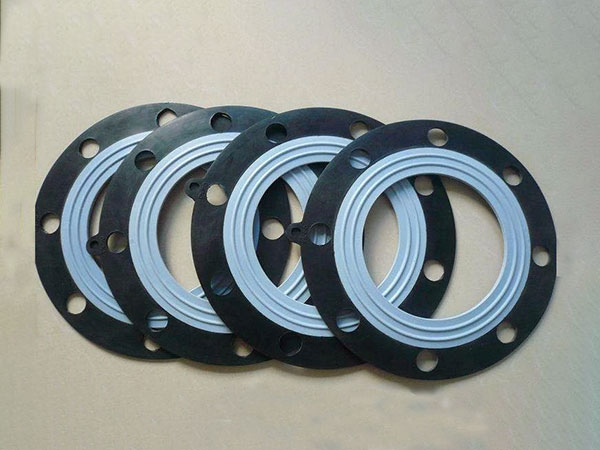
PTFE Bonded EPDM Gasket
PTFE Bonded EPDM gasket is produced with high-quality EPDM rubber and PTFE for maximum chemical and corrosion resistance. They are suitable for fibreglass, glass-lined, and steel full-face flanges. The gaskets have Low bolt torque with superior sealing, Dual, Concentric, Convex sealing rings; They will eliminate cracked flanges, reducing installation costs, while maintaining high performance. It is ideal for plastic piping systems, as well as metal or plastic-lined metal systems. Standards: ASME (ANSI) B16.5, JIS 10K, DIN2501 PN10/PN16, SABS1123, BS4504 etc
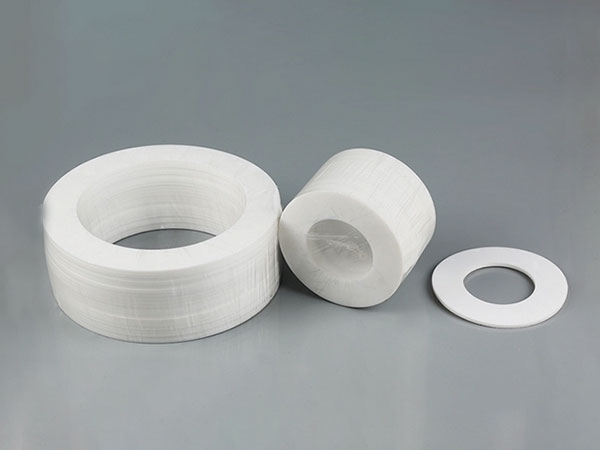
Pure PTFE Gasket
Pure PTFE Gasket is moulded or skived or cut from virgin PTFE sheets, rods, tubes or compounds etc. It has the best chemical corrosion resistance among known plastics. Without being ageing, lowest friction coefficient, wear resistance. The unloaded operating temperature range is -180~+260C.
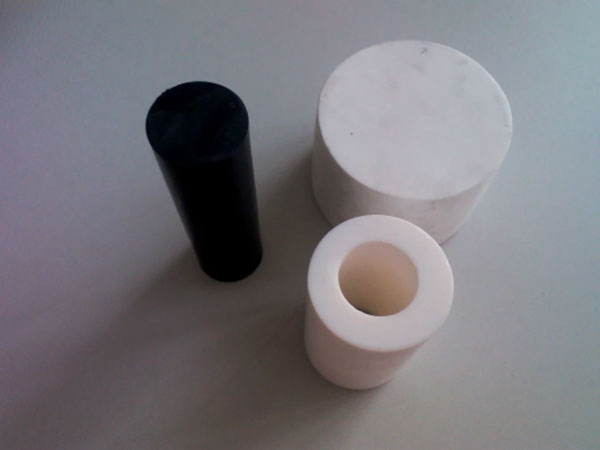
Pure PTFE Rod and Tube
PTFE Rod has Extruded or Molded two types. Moulded/Extruded PTFE Rod produced from 100% PTFE virgin PTFE materials, it has the lowest coefficient of friction of all kinds of solid materials and the best electrical properties of all plastics. They are the ideal elements for the food industry. PTFE tube made from 100% PTFE virgin PTFE material, it is suitable for use as machining stock for all kinds of chemical, electrical, mechanical components
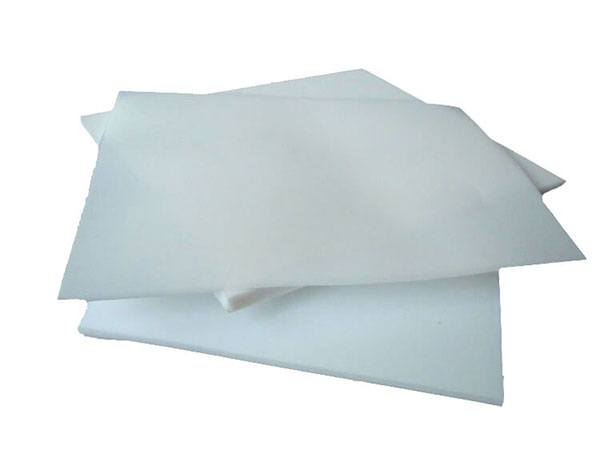
Pure PTFE Sheet
Pure PTFE sheets are moulded, skived, or cut from 100% virgin PTFE. It has the best chemical corrosion resistance among known plastics, without being ageing, with the lowest friction coefficient. It is used as sealing material, electrical insulating part, lining, oil-less lubricating materials
PTFE Products Manufacturers FAQ
PTFE Products – Definitive Guide
There is no doubt that fluoropolymers are a class of plastics with multiple properties. Furthermore, PTFE’s discovery led to the development of fluoropolymers and their numerous applications. Today, the applications of PTFE range from low-tech non-stick pan surfaces (yes! it is a smooth coating on the kitchen utensils you use in the kitchen) to high-tech exotic medical and hospital uses, including plant Enter objects, surgical instruments and test equipment, and fire-fighting equipment and other dramatic uses. Find out the properties of multifunctional polymers that PTFE offers various advantages in these applications. Learn about its characteristics, attributes and more…
1. What is PTFE?
In its most simple form, polytetrafluoroethylene or PTFE is a polymer of fluorine and carbon, with multifunctional properties. A common application of this polymer is a non-stick coating on kitchen cookware (pans, bakeware, etc.), so you can easily find it in your kitchen.
In addition to being used in kitchens, PTFE is also used in industries such as oil and gas, chemical processing, industry, electrical/electronics, and construction. It is a cost-effective solution.
The basic properties of PTFE make it an interesting material with high commercial value:
- Except for chemical resistance
- High-temperature resistance and low-temperature resistance performance
- Good electrical insulation ability in a hot and humid environment
- Light resistance, UV resistance, weather resistance
- Low coefficient of friction
- Low dielectric constant/dissipation coefficient
- Strong anti-adhesion performance
- flexibility
- Good fatigue resistance under low stress
- Food, medical and high purity grades are available
- Low water absorption
Polytetrafluoroethylene (PTFE) is a linear polymer of tetrafluoroethylene (TFE). It is manufactured by the free radical polymerization mechanism of intermittent addition polymerization of TFE in an aqueous medium.
Polytetrafluoroethylene [CF2-CF2]n has a chemical structure similar to polyethene (PE), except the hydrogen atoms are replaced by fluorine (hence it is known as a perfluoro polymer). However, it is worth noting that in practice, the preparation and use of PTFE and polyethene are completely different.
Molecular Structure of PTFE
It is the size of a fluorine atom and forms a uniform and continuous sheath around the carbon-carbon bond, thus giving the molecule good chemical resistance and stability. This uniform fluorine sheath also provides electrical inertness to the molecules.
Theoretically, the fluorine content in PTFE is 76%, and the crystallinity is 95%.
In 1938, Dr Plancott of DuPont discovered polytetrafluoroethylene for the first time “accidentally”. Thereafter, in 1947, polytetrafluoroethylene (PTFE) was made commercially available under the trademark “Teflon™” from Chemours. It is the discovery of PTFE that has accelerated the development of other fluoropolymers.
2. Typical characteristics and performance of PTFE
PTFE has granular, fine powder and water-based dispersion forms.
- The granular polytetrafluoroethylene resin is produced by suspension polymerization in an aqueous medium, requiring only a small amount or no dispersant. Granular PTFE resin is mainly used for molding (compression and isostatic pressing) and stamping extrusion.
- Use a controlled emulsion polymerization method to prepare fine powder polytetrafluoroethylene, the product is white particles with small particle size. The fine PTFE powder can be processed into flakes by paste extrusion or used as an additive to improve wear resistance or friction properties of other materials.
- Use more dispersant and stirring to prepare PTFE dispersion by water polymerization. Dispersants are used in coatings and film casting.
- As mentioned above, PTFE has excellent properties such as chemical inertness, heat resistance (high and low), electrical insulation properties, low friction coefficient (static 0.08 and dynamic 0.01), and in a wide temperature range (260 To 260°C) non-stick performance.
- Its density is in the range of 2.1-2.3 g/cm3, and the melt viscosity is in the range of 1-10gpa / second
- PTFE is one of the most chemically resistant polymers. Exceptions include molten alkali metals, gaseous fluorine at high temperature and high pressure, and a few organic halogenated compounds, such as chlorine trifluoride (ClF3) and oxygen difluoride (OF2)
The mechanical properties of PTFE at room temperature are generally lower than engineering plastics. Mixing with fillers has always been a strategy to overcome this shortcoming. Within the use temperature range, polytetrafluoroethylene is useful mechanically.
Process parameters such as molding pressure, sintering temperature, and cooling rate also affect the mechanical properties of PTFE. Variables such as the molar mass, particle size, and particle size distribution of the polymer have an important influence on the mechanical properties of the polymer.
- PTFE has excellent electrical properties, such as high insulation resistance and low dielectric constant. Due to the highly symmetrical structure of the macromolecule, it has an extremely low dielectric constant (2.0).
- PTFE has high thermal stability below 440°C without significant degradation
- PTFE material can be used continuously below 260°C.
- PTFE is attacked by radiation and begins to degrade in the air with a dose of 0.02 Mrad.
These properties come from the special electronic structure of fluorine atoms, stable carbon-fluorine covalent bonds, and unique intramolecular and intermolecular interactions between the fluoropolymer segment and the main chain.
Property | Value |
Melting Temperature (°C) | 317-337 |
Tensile Modulus (MPa) | 550 |
Elongation at Break (%) | 300-550 |
Dielectric strength (kV/mm) | 19.7 |
Dielectric Constant | 2.0 |
Dynamic Co-efficient of Friction | 0.04 |
Surface Energy (Dynes/g) | 18 |
Appl. Temperature (°C) | 260 |
Refractive Index | 1.35 |
3. Disadvantages of PTFE
Traditional PTFE has certain limitations in the application, such as:
- It is impossible to use conventional molten state processing methods, and the difficulty and cost of specific methods applicable
- Sensitive to creep and wear
- Significant dimensional changes near the glass transition temperature (19°C)
- Difficulties to join
- Corrosive, easy to produce toxic gas
- Low radiation resistance
5. The influence of fillers and additives on the properties of PTFE
The addition of fillers can improve the mechanical properties of PTFE, especially the creep rate and wear rate. Glass fibre, bronze, steel, carbon, carbon fibre, graphite, etc. are commonly used fillers.
Glass fibre has a positive effect on the creep performance of PTFE by reducing the low and high temperature creep properties of PTFE. Glass-filled compounds perform well in oxidizing environments. Further, improve the wear performance of PTFE.
Carbon reduces creep, increases hardness and improves the thermal conductivity of PTFE. Combined with graphite, it can further improve the wear resistance of carbon-filled compounds. These compounds are very suitable for non-lubricating applications such as piston rings in compressor cylinders. In addition, graphite gives polytetrafluoroethylene excellent wear properties, and graphite-filled polytetrafluoroethylene has an extremely low coefficient of friction.
Carbon fibre reduces creep, increases bending and compression modulus, and improves hardness. Unlike glass fibers, carbon fibers are inert to hydrofluoric acid and strong alkalis. Carbon fiber polytetrafluoroethylene compound has a lower coefficient of thermal expansion and a higher coefficient of thermal conductivity. These parts are ideal for shock absorbers, water pumps, etc. of auto parts.
Bronze-filled PTFE compounds have high thermal and electrical conductivity, which in turn makes these compounds well-suited for applications that bear loads at extreme temperatures.
Other fillers in PTFE are used to produce special compounds, including calcium fluoride, alumina, mica, and polymer fillers.
Generally speaking:
- Filler makes PTFE have excellent performance at low temperatures and high temperatures.
- Fillers/additives increase the porosity of the PTFE compound, thereby affecting the electrical properties-the dielectric strength decreases, while the dielectric constant and dissipation factor increase
- The chemical properties depend on the type of filler used. The chemical properties of filled PTFE compounds are generally not as good as unfilled resins.
Filler changes the electrical conductivity and thermal conductivity of PTFE
In the case of incomplete loss of physical properties, adding 40% (volume ratio) filler can make polytetrafluoroethylene (PTFE) not deformed
The effect of filler below 5% is small.
6. Popular technology for processing polytetrafluoroethylene
Polytetrafluoroethylene has a high melt viscosity and high melt temperature. Due to the rigid polymer chain structure, it is difficult to process by ordinary extrusion and injection molding methods. Compared with traditional plastic processing, its processing technology is more similar to powder metallurgy.
Sintering, pressing, stamping or paste extrusion, compression molding or isotactic molding, processing, hot stamping and extrusion of preformed powders on special machines.
- Paste extrusion, PTFE mixed with hydrocarbons, preforms before molding, used to continuously manufacture PTFE to pipe, tape, and wire insulation. Before partial sintering, hydrocarbons are vaporized
- Dispersion-metal coating, coating, crushing, dipping, casting film and fiber spinning.
- [Working range (-270°C) -200°C to 260°C(280°C)]
The performance of PTFE products is closely related to the processing technology, such as polymer particle size, sintering temperature and processing pressure. Therefore, in some specific applications where PTFE is not fully suitable, other fluoropolymers are still needed.
This led to the research of melt-processable fluoropolymers and the development of other members of the family.
7. Technical details of PTFE
Fluoropolymers have many advantages and strengths, such as non-stick, low friction, and chemical resistance. However, in order to correctly select the fluoropolymer suitable for a particular application, we have included additional technical information describing the general and comprehensive properties of the material range. In addition, other references can be found that emphasize the benefits of the industrial fluoropolymer range.
Key features of PTFE coating:
Not sticky:
Some viscous materials may adhere to the PTFE coating, but almost all substances are easily released from the surface.
Low coefficient of friction:
The friction coefficient of PTFE is generally between 0.05 and 0.20, which is related to the load and dynamic speed.
Non-stick tin:
The surface of the coated polytetrafluoroethylene is both oleophobic and hydrophobic, and it is not easy to wet. Cleaning is easier, and in some cases, the surface is self-cleaning.
Heat resistance:
The PTFE coating can work continuously up to 260°C.
Electrical performance:
PTFE coating has high dielectric strength, low loss, and high surface resistivity.
Low-temperature stability:
The PTFE coating can withstand extreme temperatures without loss of physical properties. PTFE coating can be used for low -270°C/-454°F.
Chemical resistance:
PTFE is generally not affected by the chemical environment, except for molten alkali metals and highly reactive fluorinating agents.
Definition of resin- Fluoropolymer
Fluoropolymers are known for their inertness to most chemicals, high-temperature resistance, extremely low coefficient of friction, and excellent dielectric properties that are relatively insensitive to temperature and power frequency.
Fluoropolymers are typically used for nonstick coatings for electrical/electronic equipment, plumbing, and chemical processing equipment, cookware, and other purposes. In fluoropolymers, some hydrogen atoms connected to the carbon chain are replaced by fluorine or fluorinated halides. Sometimes, other halogens, such as chlorine, are also present in the molecule.
The most common commercial fluoropolymers are:
- FEP (fluorinated ethylene-propylene) synthesized from tetrafluoroethylene [C2F4] and hexafluoropropylene [C3F6];
- Polytetrafluoroethylene (poly tetra fluoro ethylene) is made by polymerizing tetrafluoroethylene and ethylene [C2H4];
- PFA (perfluoroalkoxy) of tetrafluoroethylene and perfluoropropy vinyl ether [C3H7C4OF5];
- PCTFE (polychlorotrifluoroethylene) of chlorotrifluoroethylene monomer [C2F3CI];
- Cfe-vdf (polychlorotrifluoroethylene ethylene) synthesized from chlorotrifluoroethylene and vinylidene fluoride [C2H2F2]; E-CTFE (polyethylene chlorotrifluoroethylene) synthesized from chlorotrifluoroethylene and ethylene;
- Vinylidene fluoride monomer of polyvinylidene fluoride; vinyl fluoride monomer [C2H3F] PVF (polyvinyl alcohol fluoride).
8. PTFE Ultimate FAQ Guide
Q: In addition to PTFE, what other coatings do you use?
A: The other coatings applied are described in the coating selection.
Q: What is the largest item that can be wrapped?
A: Our largest oven is 2 square meters, and we also have a 10-meter conveyor oven.
Q: Are there many colors?
A: There are colors available, however, it must be remembered that PTFE coatings are performance coatings and therefore not designed for their aesthetic appearance.
Q: Can some geometric features be covered and not covered?
A: Uncoated areas can be realized by masking.
Q: What is Teflon®?
A: Teflon® is a registered trademark of Chemours, used in connection with products produced by Chemours’ fluoropolymer products.
Q: What is the best chemical resistance paint?
A: PFA will be the most popular choice. PFA variants have different characteristics for different applications,
Q: Can the existing PTFE coating be removed?
A: Existing PTFE coatings can be removed by replacing sandblasting media, such as crushed corn, crushed walnut shells and crushed thermosetting plastics are some options. These materials have little effect on the geometry of the part.
Q: How does PTFE stick to other surfaces?
A: PTFE can adhere to another surface through abrasive media such as aluminum oxide or the application of corrosion primer.
Q: What chemicals can PTFE resist?
A: PTFE material is inert in nature. They are only affected by molten alkali metals, fluorine, and chlorine trifluoride under high temperature and pressure.
Q: What kind of temperature can PTFE withstand?
A: PTFE is rated for continuous use at temperatures up to 260°C. It can also be exposed to high temperatures for a short time.
Q: What does the coefficient of friction mean?
A: This is a quantity used to calculate the friction between two parts. Friction decreases as the value decreases.
Q: What is molybdenum?
A: Moly is the common abbreviation for molybdenum disulfide. There is a beneficial additive to improve the lubricity of the PTFE coating and maintain a higher load.
Q: What is a technical data sheet?
A: This is detailed information mainly for industrial and commercial users. The product description, characteristics and advantages, application methods, and some properties of PTFE coatings are introduced in detail.
Q: Why should I choose PTFE coating?
A: All solid materials have a lower friction coefficient than Teflon. Its wear resistance is adapted to harsh environments through inorganic fillers such as glass fiber, carbon and graphite. PTFE has excellent anti-stick and non-wetting properties, and it retains its excellent properties even at low temperatures because it is chemically pure and inert.
Q: How is PTFE coating applied?
A: PTFE coating is applied by spray method, however, powder such as PFA can be applied electrostatic method.
Q: What is the thickness of the coating?
A: The thickness of the coating depends on the number of coatings, however, the average thickness of a single coating system is between 20 microns and 25 microns.
Q: What substrate can be coated?
A: The most suitable substrates are clean stainless steel, steel and aluminum, and most other metal substrates. Substrates that attract oxidation, such as copper, brass, and zinc, will require additional surface treatment. The coating is possible on other materials, such as glass, plastics, and elastomers, although some elastomers do not work properly at high temperatures.
Q: Will the paint conceal and conceal surface defects?
A: The coating will follow the contour of the substrate surface.
9. Teflon Coating Process
The term “polytetrafluoroethylene” refers to polytetrafluoroethylene homopolymers and polymers made by copolymerizing tetrafluoroethylene with other monomers. It also includes vinyl fluoride polymers containing other halogens, and polymer mixtures of different compositions. Polymers can have different chain lengths (molecular weights) and molecular weights. If desired, other particles, such as coloured mineral particles, may include PTFE particles.
PTFE bonds to the substrate via mechanical keying between the PTFE and the surface of the substrate. The diameter of the PTFE particles is preferably less than 100 microns, more preferably less than 50 microns. Especially recommended are PTFE particles with a maximum diameter of fewer than 30 microns.
In conventional or air atomized spraying, the coating is delivered to the spray gun by siphoning, gravity or pressure. When the gun is triggered, the coating will flow through the nozzle like a fluid. When the fluid leaves the nozzle, the compressed air from the center of the nozzle surrounds the fluid in a hollow cone, breaking the coating into small droplets, and transferring the velocity to it. The additional compressed air ejected from the nozzle further breaks the water droplets into an oval shape.
In electrostatic coatings, the fluid is atomized and then becomes negatively charged. The coated part is electrically neutral, making this part positive with respect to the negative coating drop. The coated particles are attracted by the surface and held there by the difference in charge until they are cured.
In an electrostatic spray gun, the droplets get a charge from a charged electrode on the tip of the spray gun. The initial momentum of the charged particles is obtained by the fluid pressure/air pressure combination. Electrostatic spraying provides high transfer efficiency (65% to 95%) and excellent edge coverage. The attraction between the paint drop and the part is strong enough to cause the paint to be over-sprayed and miss the part bending, which contributes to high transfer efficiency.
Electrostatic applications do not cover the recessed area (Faraday cage) and non-electrostatic applications. The charged droplets tend to be attracted by the edges and sharp edges of the grooves instead of penetrating to the bottom.
All conductive materials (such as power supplies, containers, spraying equipment, etc.) near the spray area must be grounded to prevent static electricity from accumulating. All hangers, conveyors, etc. must be kept clean to ensure conductivity to the ground. Charge accumulates on surfaces that are not grounded. Operators grounding these surfaces may experience severe static shocks.
Traditional air spraying is the oldest spraying process. It provides the best control of spray pattern and degree of atomization. This system can produce the best atomization effect, so it can also produce the best polishing effect. Traditional spraying technology can also spray the widest range of coating materials among the four technologies.
While PTFE particles can be applied to the applicator surface in a dry state, some people prefer to “apply liquid dispersion to the applicator surface” for convenience. Preferably, the dispersing solvent has sufficient volatility to evaporate almost immediately, leaving the particles in a substantially dry state.
Polytetrafluoroethylene is very resistant to chemical attack, and the surface free energy of solid polytetrafluoroethylene is very low. This means that liquids do not easily wet solids, and other solids do not adhere firmly.
With these properties, PTFE can be used as a protective coating in a wide range of applications, from non-stick cookware to engineered products. The method of coating polytetrafluoroethylene is to disperse low-molecular-weight polytetrafluoroethylene solids on a substrate, suspend them in a suitable liquid such as a solvent or water, called a carrier, and then evaporate the carrier.
In order to increase the uniformity of the coating, this coating is sometimes sintered or even polished. However, the coating formed by this method can be used as a single coating application, such as in a mold release application or as a mold release layer. This application method can be applied to a wide range of substrates and produce a tough and durable PTFE coating. Some PTFE coating systems can be multi-coat types, including primer and middle coat applied before the final coat. The typical film thickness is between 10 and 100 microns, such as 20 microns. To 50 nanometers thick. The usual feature is that the water-based PTFE coating is effective self-limiting thickness. However, PFA (powder) coatings can deposit additional thickness.
10. PTFE Formula Guide
This section introduces the background of some elements related to the formulation and provides insights into the differences in the performance and appearance of coatings. Teflon coating formulations are created to produce coatings that operate in different environments, as well as to produce films that can be sprayed. Manufacturers of Teflon® products, such as Chemours and Whitford Ltd, which manufactures Xylan® products, continue to develop and reformulate PTFE coating systems to optimize their functional performance.
The choice of material provides the required properties to suit different applications. Binders are added to the range of “non-stick” coatings to ensure that the coating adheres to the substrate. The pigments not only give the coating color, but may also mask surface irregularities. Additives are used to assist the spraying of materials, especially to help the flow and sedimentation of the product on the substrate to prevent sagging of the wet coating.
Take a closer look at the ingredients
Binding. These products provide adhesion to the substrate and are particularly important in one-layer coating systems and primers. Due to the curing temperature of fluoropolymers, options may be limited, including:
- PAI: polyamide-imide
- PES: Polyethersulfone
- PPS: polyphenylene sulfide
- Epoxy
During the curing stage of the coating, this binder will allow the migration of PFTE, mainly rising above the binder, paving the way for the properties of the coating on the “contact surface”.
Paint. The formula contains various products, some of which are as follows:
- Carbon black
- Titanium oxide
- Filling agent
- Chromium oxide
- Mica flakes
- Dark blue
- Aluminium foil
These products, alone or together, can produce a very diverse range of colors. However, it must be emphasized that PTFE coatings are not designed as a decorative products. Pigments play an important role in tandem with other products to produce the final coating system.
Solvent. These products are added not only to assist the “chemical” reaction during the curing process but also to act as a carrier to spray the product in a way that will produce a uniform coating. The solvent can be a pure solvent or a solvent mixed with water. Such water-based coatings become more and more important when encountering environmental problems. Generally, water-based materials are used in coating systems for cooking appliances and industrial applications. Solvent-based coating systems are used for baking utensils, electrical appliances and industrial applications.
Additives. The manufacturer adds materials to the formulation to give the coating specific properties, resulting in different properties. These additives can stabilize the material and enhance the fluidity of the material during application. Additives can also change viscosity. Most importantly, additives can reduce foaming and reduce product sedimentation. Another key additive is to eliminate the “fish-eye” phenomenon in the coating so that the coating can be wet.
Fluoropolymer coatings are not pure fluoropolymers. Since fluoropolymers are soft, they alone cannot provide good adhesion. Fluoropolymer coatings include a binder resin, which acts like glue, holding the fluoropolymer in place and strengthening them.
The most commonly used fluoropolymer resins are PTFE (polytetrafluoroethylene), FEP (fluorinated ethylene propylene) and PFA (perfluoroalkoxy). FEP and PFA are commonly used as thick film coatings. Polytetrafluoroethylene is not melt-processed, and is mainly in the form of particles as a part of the dispersion. PTFE is the best dry film lubricant. The content of PTFE relative to the binder resin determines the lubricity of the coating. Tetrafluoroethylene does not affect the corrosion resistance of chemicals.
11. Application of PTFE and Filled PTFE
Application of PTFE and filled PTFE in fluid treatment:
Its extraordinary chemical resistance and high heat resistance to almost any service condition make PTFE and filled PTFE products a popular material in the chemical, pharmaceutical, petrochemical and petroleum industries. The main applications include:
Polytetrafluoroethylene (PTFE) sealing material: gasket, O/D/V/U ring, general steel wire rope, crescent ring for glass pipe.
- PTFE expansion joint: bellows
- Teflon ball valve seat-seal
- PTFE diaphragm for diaphragm valves and diaphragm pumps.
- PTFE experimental utensils: beaker, stopcock.
- The PTFE sleeve of the plug valve.
- PTFE mechanical seal for pump
- PTFE impeller/pump body.
- Teflon pipes and hoses.
- PTFE lining of reactors, storage vessels/pipes and flanges.
- Teflon thread sealing tape.
- The PTFE liner/disc of the butterfly valve.
Most of the products produced by Standard Fluoromers pv. Ltd. are PTFE and filled PTFE components/grades.
Application of PTFE and filled polytetrafluoroethylene in fluid treatment
Application of PTFE and filled PTFE in mechanical engineering:
Due to its unique surface friction/wear properties, PTFE and filled PTFE products have many applications in the mechanical and civil engineering industries, such as machine tools, air compressors, bridge bearings, hydraulic and pneumatic seals. The main applications include:
- PTFE low-friction bushings for machine tool guides and slides.
- PTFE piston ring for dry air compressor.
- PTFE low-load high-speed bearings.
- PTFE tape and piston seals for hydraulic and pneumatic actuators.
- PTFE hysteresis friction washers for automobile clutches.
- Teflon bridge support cushion.
- PTFE bearings/pads for sprinklers.
- Teflon pipe supports bearing pads.
- PTFE railway bogie bearings.
- PTFE bearing for conveyor belt
- PTFE gearbox wiper ring.
- PTFE bearings/gaskets for actuators.
- Polytetrafluoroethylene (PTFE) railway bogie support pads/wear strips/bearing pads.
- Support pads/wear strips/bearing pads in machine tools and equipment
Most of these products produced by Standard Fluoromers pv. Ltd. contain PTFE and filled polytetrafluoroethylene components. Application of polytetrafluoroethylene and filled polytetrafluoroethylene in mechanical engineering The application of polytetrafluoroethylene and filled polytetrafluoroethylene in electronic and electrical engineering:
PTFE and filled PTFE products are mainly used in electrical and electronic engineering industries, such as electric switch gears, capacitors, traction motors, traction generators, etc., mainly due to their outstanding electrical insulation properties.
The main applications include:
- PTFE nozzle for SF6 circuit breaker.
- Ultra-thin sintered insulating tape for PTFE tractor.
- Films of PTFE capacitors.
- Teflon brush holder.
- Teflon thin-walled noodle tubing heat insulation in aeroplanes and space vehicles
- Fail-safe application of PTFE ultra-thin tape.
- PTFE Barb insulator.
- PTFE heat shrinkable tubing insulation.
- Teflon connector.
Most of the products produced by Standard Fluoromers pv. ltd. are PTFE and filled PTFE components.
12. Innovation of PTFE
Teflon coatings, also known as Teflon® coatings and Xylan® coatings, are traditionally applied to cookware first and then to engineering products. However, there are other applications for Teflon® and Xylan® coatings. Through “thinking outside the box” or “blue-sky thinking”, whatever you call it, PTFE applied coatings have developed technologies and procedures to bring Teflon® and Xylan® coatings to a new level. By evaluating every question requested by customers, PTFE applied coating expands the range of potential applications and enables the coating to function. These differences are reflected in product performance, cost-effectiveness and customer satisfaction.
PTFE Applied Coatings has more than 40 years of engineering and coating experience. We are proud of our discovery of new and innovative methods to enable Teflon® and Xylan® coatings to be processed and applied to engineering components. Non-metallic substrates are now the sight of PTFE coatings, enhancing the properties of materials such as Viton, nitrile, glass, polyurethane and other composite materials such as carbon fiber. In addition, materials such as Inconel, brass, and copper, which were previously considered to be difficult to apply with PTFE coating, are now in the scope of coatings.